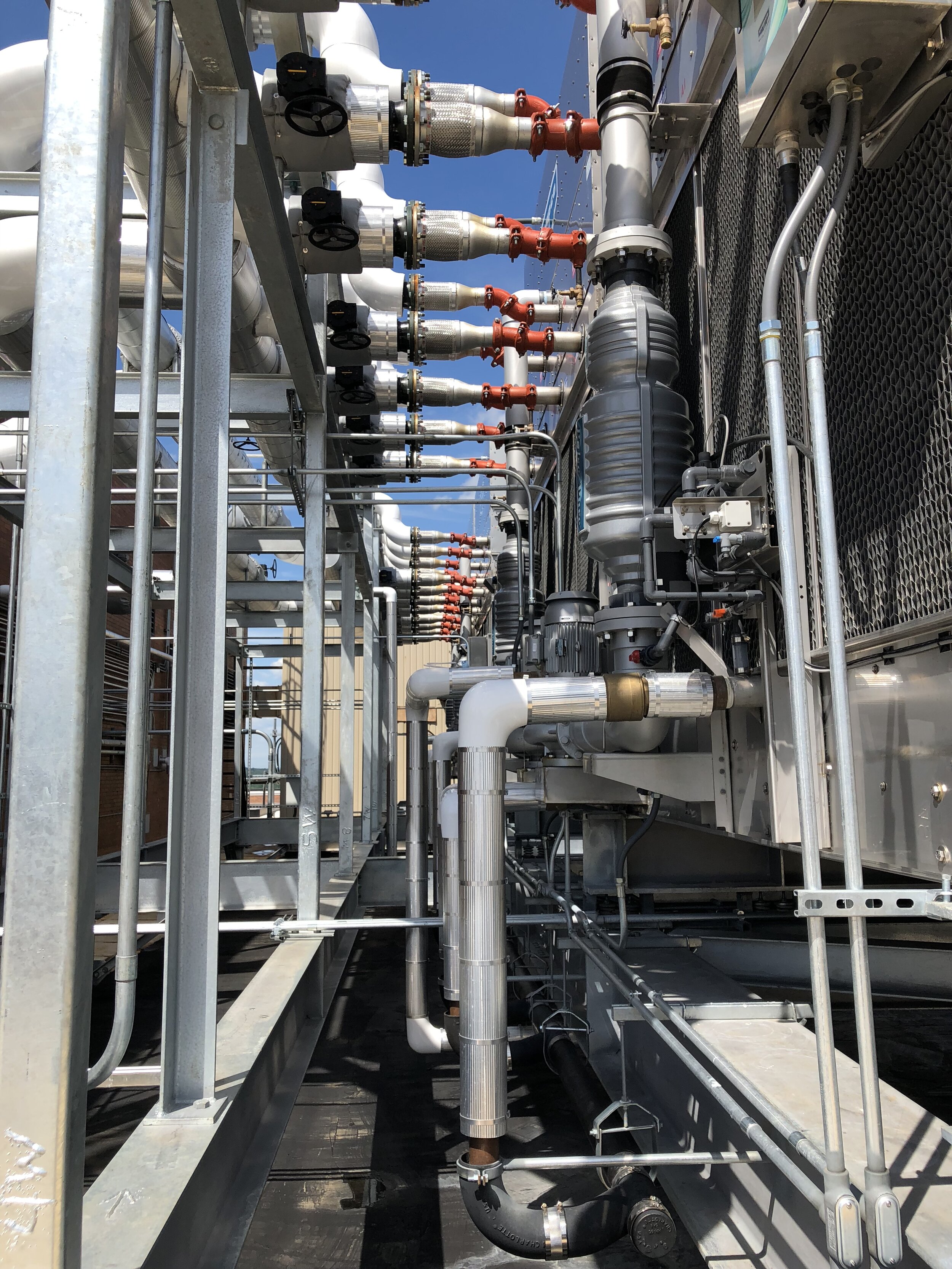
Quality Control
Our plan of action addresses four key areas as follows:
Pre-Work Coordination:
An in-house pre-work meeting is held prior to start of work on a project. The assigned Project Manager, Superintendent, Project Engineer, Safety Director and Quality Control Staff will attend this meeting. The purpose of this meeting is to ensure there are no misunderstandings concerning quality as well as, technical requirements of the contract work. As a minimum, the following items will be reviewed at this meeting:
Contract Documents and Requirements
Submittal Procedures and Required Information
Availability of Required Materials and Equipment
Purchasing Plan
Test Inspections and Records
Safety and Environmental Precautions
Initial Inspection(s):
Upon completion of a reasonable amount of the work, our Quality Control Manager, will, as a minimum, inspect the following items:
Workmanship to Insure Quality Standards
Conformance to Contract Documents and the Approved Submittals
Conformance to Applicable Building Codes and Authorities
Results of Daily Inspections and Testing Methods
Status of Shop Drawings and Updated As-builts
Follow-Up Inspection(s):
The DMI Quality Control Team will continue to monitor the work on an ongoing basis until the work is completed. This is to assure the continuing conformance of the work and the workmanship standards established during the pre-work meeting and initial inspections.
Project Close-Out:
During the project close-out process, the DMI Quality Control Manager will inspect the following items:
Test Records and Quality Control Reports
Daily Reports and Weekly Safety Meeting Minutes
Pre-Punch list Inspections
As-Built Documents
Operations and Maintenance Manuals